- How do you define green building within the construction industry, and how well aware of the construction industry is towards the ideology of green building?
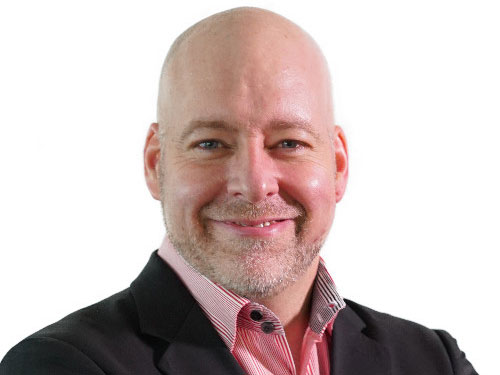
The buildings and skyscrapers in which we work, live, and play today produce a significant amount of carbon emissions which have far-ranging environmental and climate impacts. According to the World Green Building Council (WGBC), the building and construction industry is one of the largest contributors to carbon dioxide emissions β pre-pandemic figures estimate that building operations and construction contribute 38% of total global energy-related CO2 emissions.
Enter βgreen buildingsβ: they help reduce or eliminate this negative impact to our environment β whether through technology or improved operation workflows during the construction process or by tapping into energy-efficient solutions, renewable energy, and intelligent energy management systems throughout the buildingβs lifecycle.
The idea of green buildings isnβt new to the industry and has gained prominence in recent times as sustainability became a larger priority. With the construction and building sector having the largest potential for significantly reducing greenhouse gas emissions compared to other major emitting sectors, fostering greener buildings can generate many environmental, economic, and social benefits to businesses, consumers, and the general public.
Within the Asia Pacific region, Singapore is cementing its position as a model of green buildings. With the launch of the Building Construction Authority (BCA) Green Mark scheme in 2005 to foster the adoption of green buildings, followed by the introduction of the Singapore Green Building Masterplan (SGBMP) that aims to have 80% of all buildings in Singapore be green by 2030, the nation is well on its way to a greener building landscape.
2. As of now contractors and developers are still not fully aware of the indirect impacts of the construction process on the environment, such as, an environmental revolution is needed in the industry. With the context above, who should be leading the ideology and how should they proceed with it?
For a start, more emphasis needs to be placed on education to drive greater awareness of the environmental impact at each phase of the construction process. But change will not happen overnight, and itβs a challenge that requires a concerted effort from all industry players.
Government bodies play a key role in rolling out regulations and policies that support the construction industry in its sustainability journey. This involves developing policies and implementing programs that provide a sound balance between regulatory instruments (e.g. building codes and standards), incentives (e.g. financing schemes and credits), and information and talent development efforts (e.g. training courses and workshops).
In Singapore for instance, the SGBC (Singapore Green Building Council) Certification scheme implemented in 2010 acts as a benchmark when developing more sustainable infrastructure for the country. SGBCβs tool for assessing the quality of green infrastructure is called the Green Mark Scheme and operates through the accumulation of points that determine a projectβs Green Mark rating. The more points, the higher the rating under the Green Building Plan Initiative. The certificate also serves many benefits to businesses who wish to develop greener infrastructure, including greater awareness of their green products and services, industry-recognized credibility, and enhanced access to global markets.
The SGBC has also made available workshops and training programs to enable the sharing of ideas and information amongst construction professionals, with the idea that a green revolution is a shared responsibility between governments and private enterprises. Through the sharing of ideas and information via workshops and training, more construction businesses are given the necessary tools to create a more sustainable future.
Concurrently, construction businesses have an increasing responsibility to leverage technology to address the challenges that stand in their path toward greater sustainability. For instance, unified construction platforms can enable real-time access to critical project information, improve productivity and collaboration, and simplify communication among all stakeholders across the construction project. This can help reduce carbon emissions and landfill waste through better material use planning, drastically reduce rework, as well as reduce site visits. When processes are automated and silos are eliminated, the industry can make better, more informed decisions that positively impact the environment at large and add value for all stakeholders.
3. It was mentioned in the email that Procore has integrated EC3 (Embodied Carbon in Construction Calculator) into the platform. How and what will the platform be able to provide commercial, economic, and environmental benefits to the public?
Embodied carbon refers to emissions produced during the construction process β from raw materials extraction, manufacturing, and transportationβthrough to the demolition phase. For instance, the transportation of huge volumes of building materials requires multiple trips to and from construction sites. This creates a multiplier effect for greenhouse gases, continuously adding to the constant production of embodied carbon.
In partnership with Building Transparency, Procore enables its users to leverage the Embodied Carbon in Construction Calculator (EC3) tool to benchmark and assess the carbon footprint of their projects. This allows users to estimate each projectβs embodied carbon emissions and gauge alternatives during the initial design stage of the construction process. Ultimately, EC3 enables stakeholders to provide commercial, economic, and environmental benefits to the public as the platform thrives through the interaction of both customers and organizations to help reduce carbon emissions in the construction industry. By tracking and benchmarking construction emissions before projects take place, EC3 can help transform the way we construct buildings and filter materials that emit greenhouse gases.
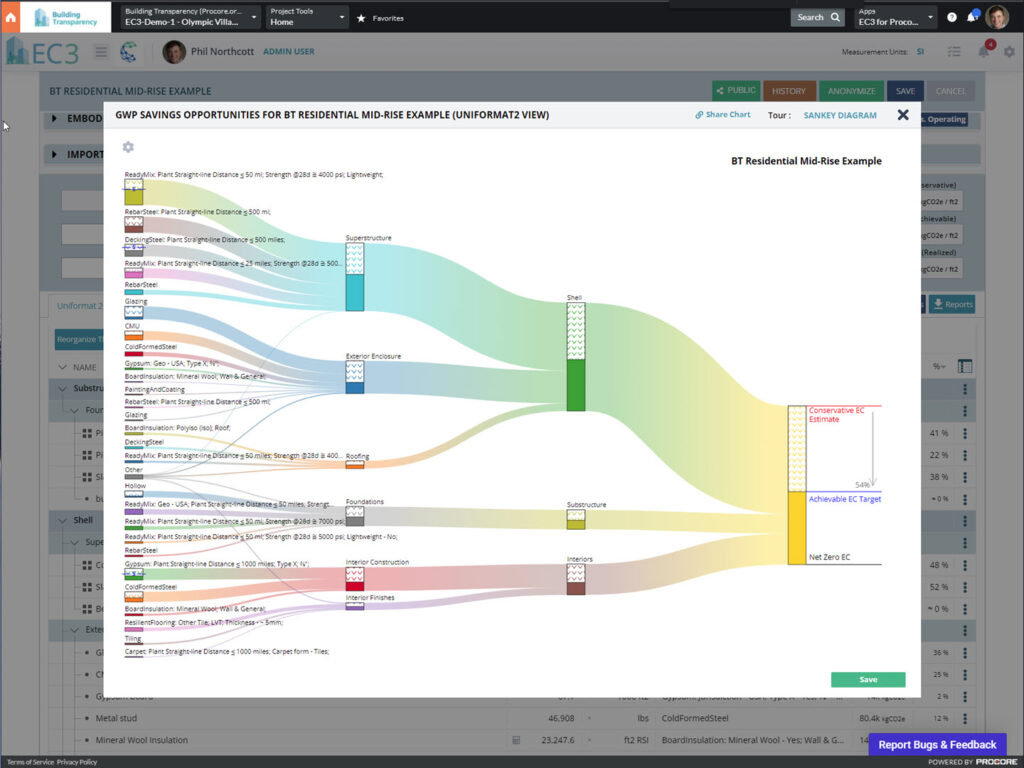
4. It is a widely known fact that the implementation of environmental technology is still relatively hard to achieve in most industries due to several obstacles in the way. Would you kindly share your insights on the obstacles to implementing green technology in the construction industry, and what should be done in order to close to the implementation of the aforesaid technology?
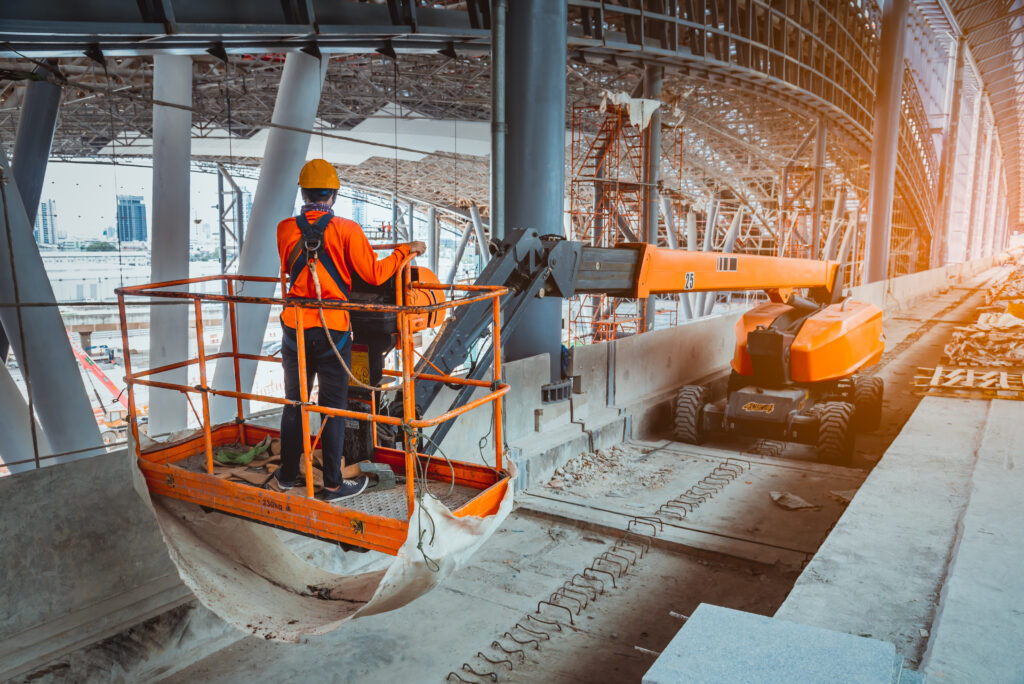
Although sustainability is regarded as a competitive differentiator within the industry, implementing greener technology often comes at a price driven by increasing government regulations to the added costs associated with more sustainable material. These challenges are often top of mind among industry professionals when it comes to designing and building green.
A key opportunity exists in rethinking workflows and processes that drive greater project efficiencies and directly contribute toward greener building practices. Case in pointβthe construction industry has been widely regarded as a laggard in the adoption of technology. However, the problem doesnβt stem from trying to implement technology but rather from trying to make an application fit the construction industry versus using technology that is purpose-built for construction. These overly generalised solutions, while able to address some challenges to some extent, fail to solve the pain points faced by everyday usersβthe people in construction.
To tackle these issues, Procoreβs all-in-one construction platform is purpose-built for construction, by construction experts, to provide the foundation for smarter construction. The April 2022 announcement of EC3 with Procoreβs cloud-based software additionally enables construction leaders to reduce embodied carbon emissions, and make informed decisions about materials and processes. Bringing all the different stakeholders onto one platform also ensures everyone is looking at the same data and information, and tracking against the same goal. This helps eliminate miscommunication or misalignment, often the cause behind costly wastage, such as rework and project delays.
5. Sustainability is a key factor when we are talking about green building, but modern-day construction material, even though improved, is still not up to the standard to be called a sustainable material. As such, in your opinion, what are the sustainability challenges that are in the industry, and what are the approaches the industry has used to tackle this problem?
In recent years, major efforts and advancements involving greener construction have occurred, with countries developing certifications and providing financial incentives for the development of green building materials and design. However, the higher costs attributed to using green building materials are a key hindrance holding many companies back from more fully adopting sustainable practices. Research shows that the base cost of a green building can be approximately 16% higher than a standard building. Technology and continuous innovation can certainly help to close this gap.
Beyond utilizing sustainable materials, one of the key measures that would make a significant impact on reducing carbon emissions in the construction process would be to reduce the amount of rework that happens during projects. Ultimately, this leads to improved resource efficiency and lower wastage of materials.
To reduce rework, the industry needs to relook its reliance on paper for tracking records. In a recent report by Procore, it was found that 36% of construction businesses in APAC continue to use paper to track and manage environmental records. Relying on manual processes often leads to erroneous data across multiple locations, delayed site-to-office communication and communication silos. Not only are these methods not mobile, but with no document version control or single source of truth, teams are often left using outdated drawingsβan easy recipe for quality issues and rework.
The integration of construction management technology can help to tackle the significant amount of rework on construction sites. By aligning stakeholders onto one platform, team members can collaborate and communicate frictionless, decreasing the amount of rework and subsequently aiding in the overall goal to become more sustainable.
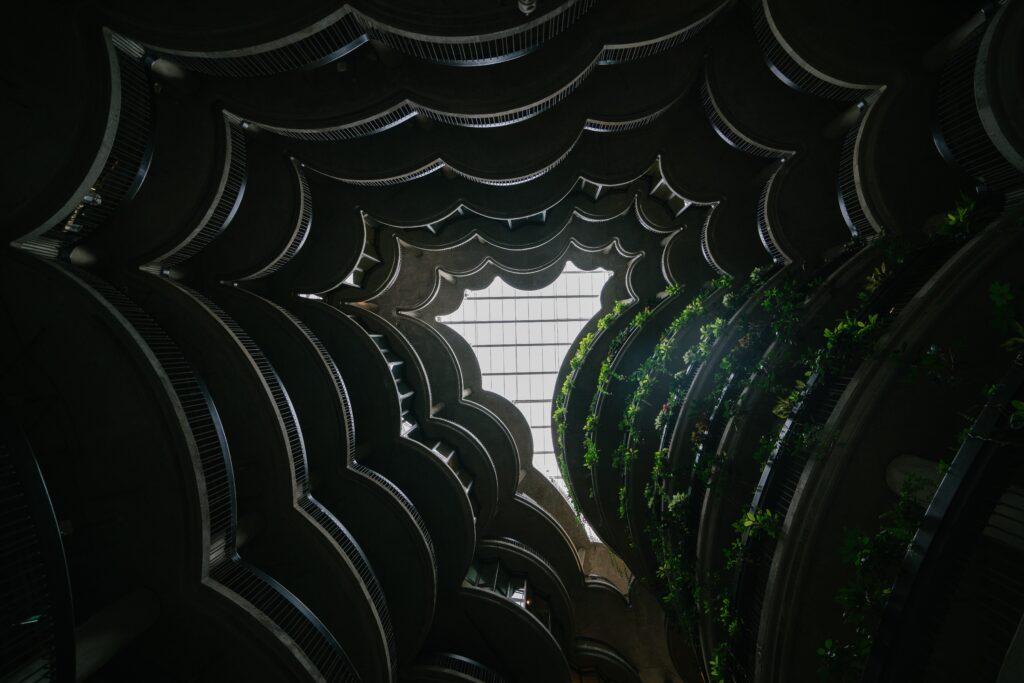